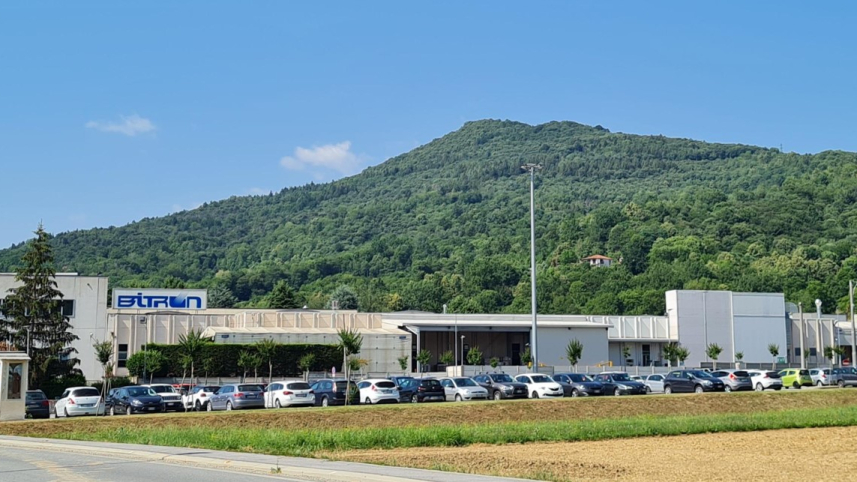
Driving Innovation: Insights from Bitron Rossana’s Plant Manager
In this interview, we speak with Umberto Rulfi, the Plant Manager of Bitron's Rossana facility. Discover how the plant has evolved over the years, the trends shaping its future, and the initiatives driving its success. Join us for an insightful conversation about the dynamic developments at the Rossana plant.
How has the Bitron Rossana plant's production and technological capabilities changed over time?
In the late 1970s, Bitron Rossana plant began making car relays. Even then, manufacturing was based on metal blanking, injection moulding and co-moulding, assembly, and testing technologies, which are still used in the factory today. This demonstrates that the operations were marked from the start by a strong verticalization of production processes, with the goal of achieving an appropriate balance between manufacturing and purchasing. Finally, the desire for added value, which still defines industrial strategy today, was evident from the start.
Over time, the product families have expanded. Working almost solely in the automobile industry, we have created products for important Italian, French, and German customers. Today, our components are supplied to all major European OEMs, and we are proud to also have a business relationship with a major Japanese OEM.
These technologies have been in use for a long period and have gradually been developed to the current stage of automation. The painting of plastic components and the application of symbols through the use of laser technology have been practiced since the 2000s. Assembly plants have experienced a significant shift from mostly manual handling to modern and actual automated car assembly lines since the 1990s. This has led to constant changes in working methods, which today involve less manual labour while at the same time require more specialized professional skills.
Which trends in the automotive market are relevant and have a strong influence on the current and future of the plant?
The Rossana plant produces almost exclusively HMI components integrating switches, touch sensors and displays. Those components are the physical interface between the driver or passenger and the various controls and services in the car. Besides these functions, the HMIs must offer aesthetic, comfortable sounds and visual feedback, all features that contribute to the appeal and finally to the market success of a vehicle.
The most influential market trends that we see are the advent of displays in HMIs and, more interesting for us, the development of HMIs integrated into continuous surfaces, with new visual feature like “ghost effect” where a function appears only when needed then disappear under the surface, and aesthetic appearance using glass or wood.
At this specific historical moment, we are experiencing a coexistence between two complex systems: the thermal car and the electric car, a new solution that is looking for its place in the mobility market. This situation has led to the creation of new product families alongside the existing ones; an example of this is the e-latch, which is used for electric opening of car doors.
Which initiatives have been put in place to increase the sustainability of the plant on an environmental basis?
The current efforts to mitigate the environmental impact of the plant are directed in three directions.
The first project concerns the reduction of natural gas consumption for both uses: heating and painting process. The boilers were replaced with two latest generation condensing heat machines, and, by replacing the afterburner ceramics, the consumption of the painting equipment was almost halved.
The second important step of intervention is a formal energy analysis of the systems. We have decided on various improvement actions regarding electricity consumption, and we have introduced greater attention to internal sharing of objectives with colleagues, the result is an increase of feedback ideas. One above all is the automated slowing down of assembly equipment when not in use.
Finally, the third element of sustainability that is practiced at all industrial levels is the continuous search for ways to reduce industrial water consumption.
Another possible future solution is a photovoltaic system with the capacity to generate 14% of the Rossana plant's annual energy consumption.
Are there any new strategic objectives that will be relevant to the future course of the Rossana plant?
The strategic goals originated from Bitron's mission are also evolving; therefore, innovative production is critical to guarantee the continuity of a business, as both the product and the technologies used in its production must be innovative. The innovation develops combining lean to smart when describing the features of technology applications and excluding unnecessary complexity or lack of flexibility. We identified two long-term strategic plans that will affect the future way forward for the plant: the development of integrated automatic three- and four-material moulding and the planning to add UV coating.
Notably, the diversification of the customer base is confirmed among the company's strategic objectives.
Which are the major components in which Bitron Rossana’s very specialized?
Very high volumes of door and console modules are present in the portfolio, both with and without active electronics, and these are very various in terms of their aesthetic features, such as glass effect with UV coating, black panel effect, backlighting with ghost effect, etc.
Besides the product with all its features, Bitron offers a wide service in terms of logistics. This is based on an ever-changing purchasing and supply management approach.
What are some of the strategies that you use to inspire and entrench employees in the pursuit of the company’s vision and missions?
The involvement is the most favourable approach for motivating employees. We have adopted “regular communication” as an overall engagement framework for years. It is methodical, continuous and repeated. Regular communication, if used properly, allow for information, goals, strategies, and concepts to be passed along the vertical hierarchy, constantly raising awareness.
The overall objective is to empower the firms to institute internal accountability, the first steps are being taken and are showing very positive outcomes. It is a long journey and not a short walk, but the path ahead of us is fully clear.
Do you solicit feedback from your employees, and how do you not only collect it but also use it to strengthen operations and the work climate?
More and more awareness assessments are being conducted for all plant staff with the latest in health and safety. These topics are very relevant and, when discussed, lead to a pull toward evolution and to a visible change of habits.
Previously held about once every two or three months, these meetings are now being held monthly, in order to increase support to our employees and as a way to share feedback with each other on both the work climate and technical issues that may arise in the operation.
The keys to success are transparency, accountability, and a willingness to explain decisions-a process that is onerous and involves risk but which, in the long run, produces growth in awareness and fosters effective communication.
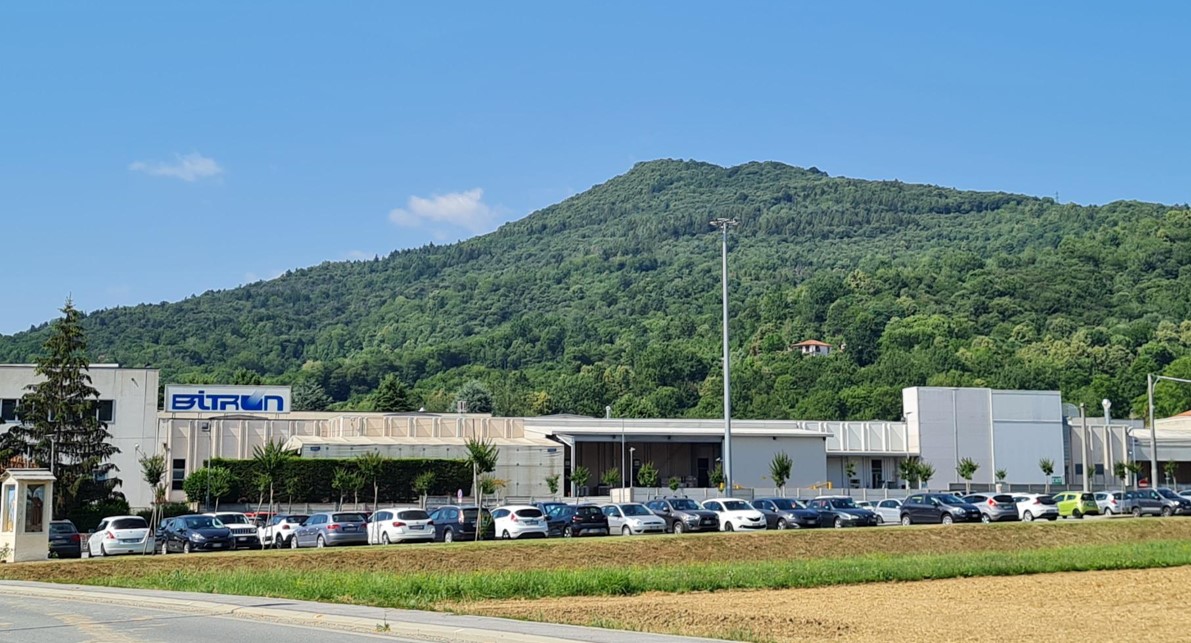
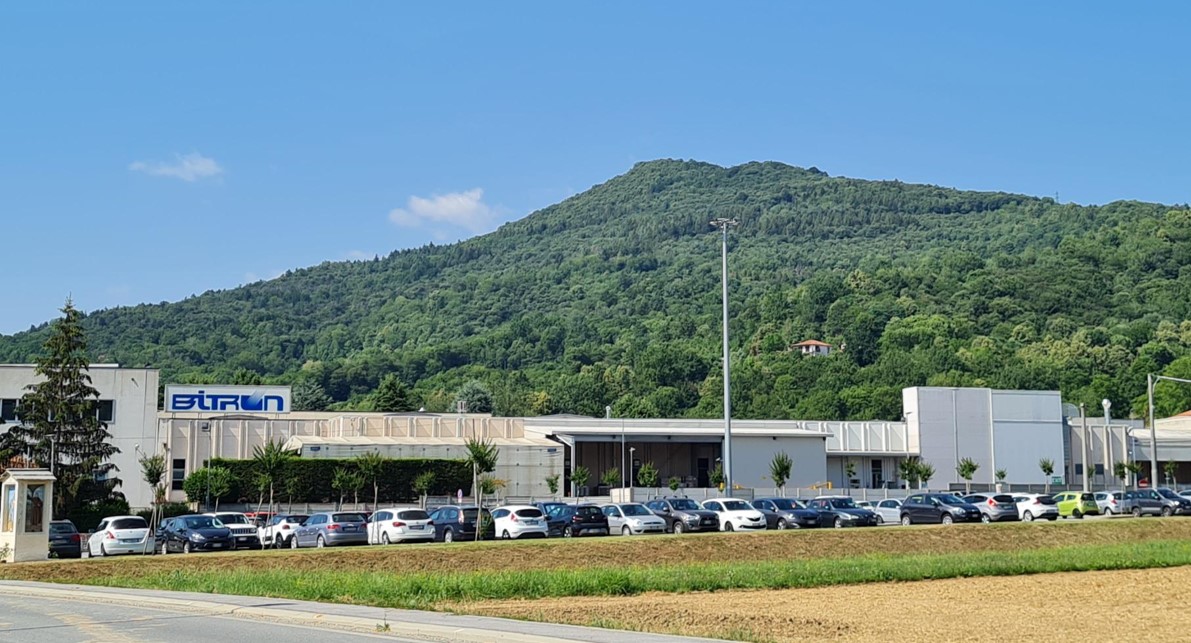
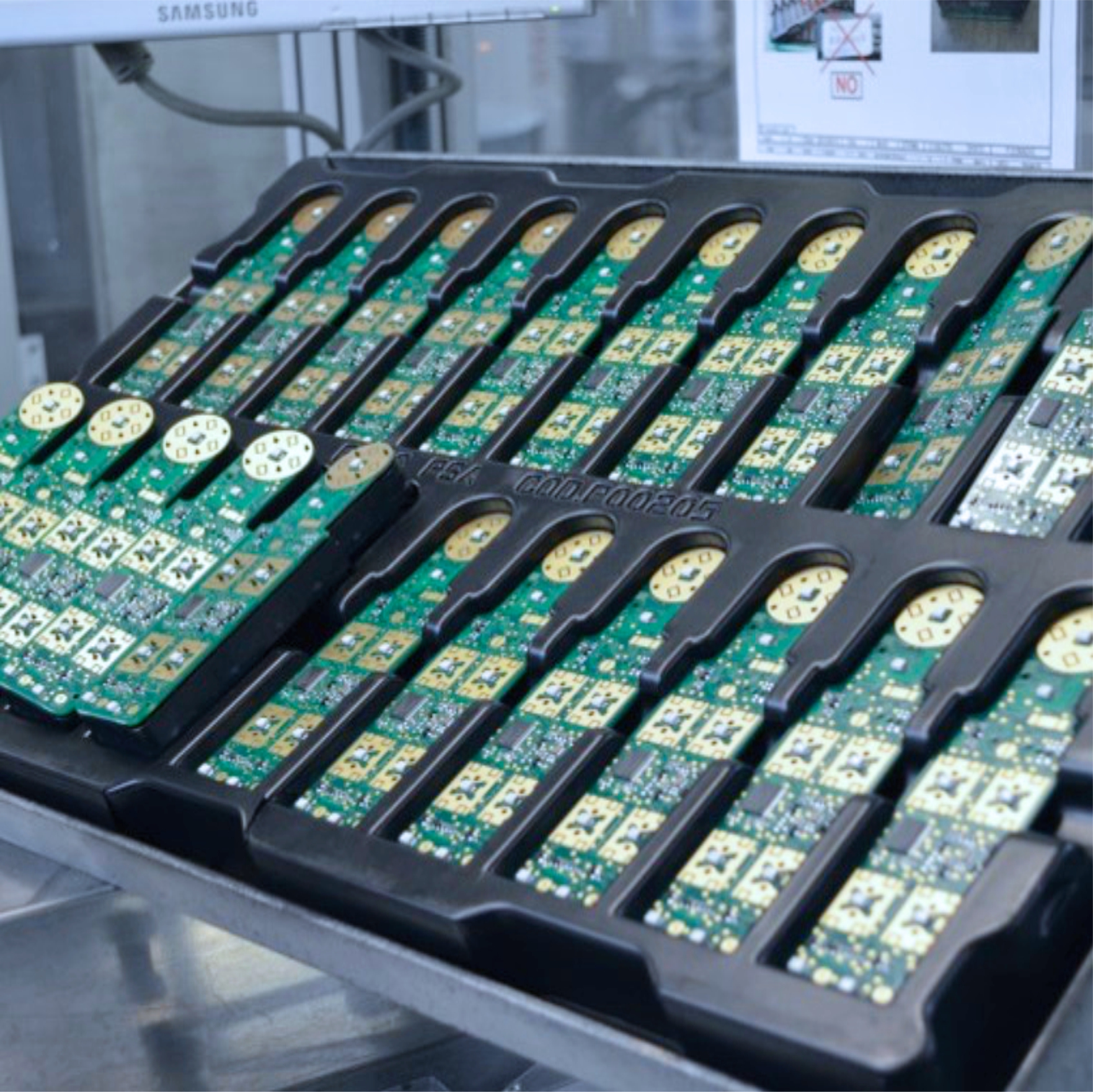
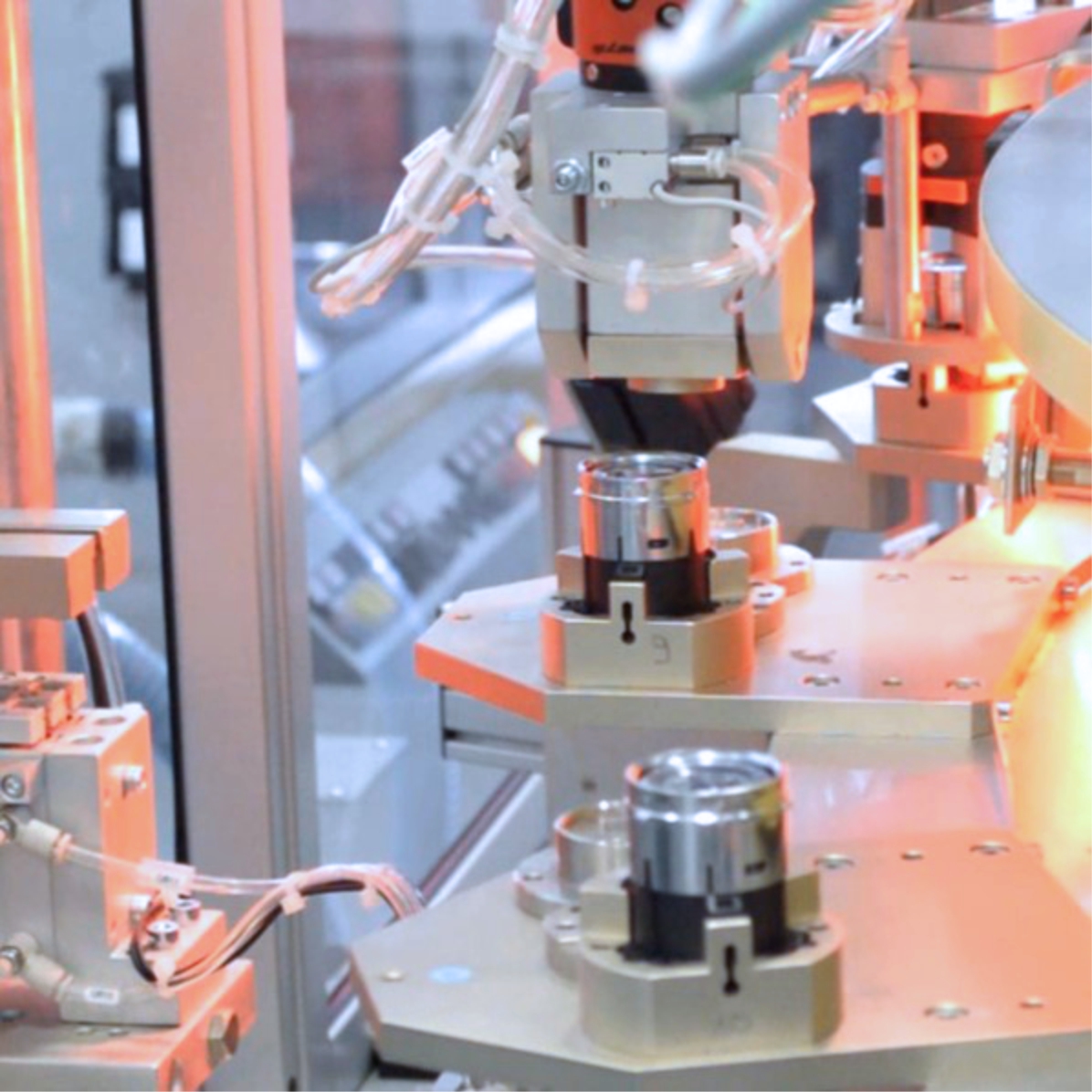
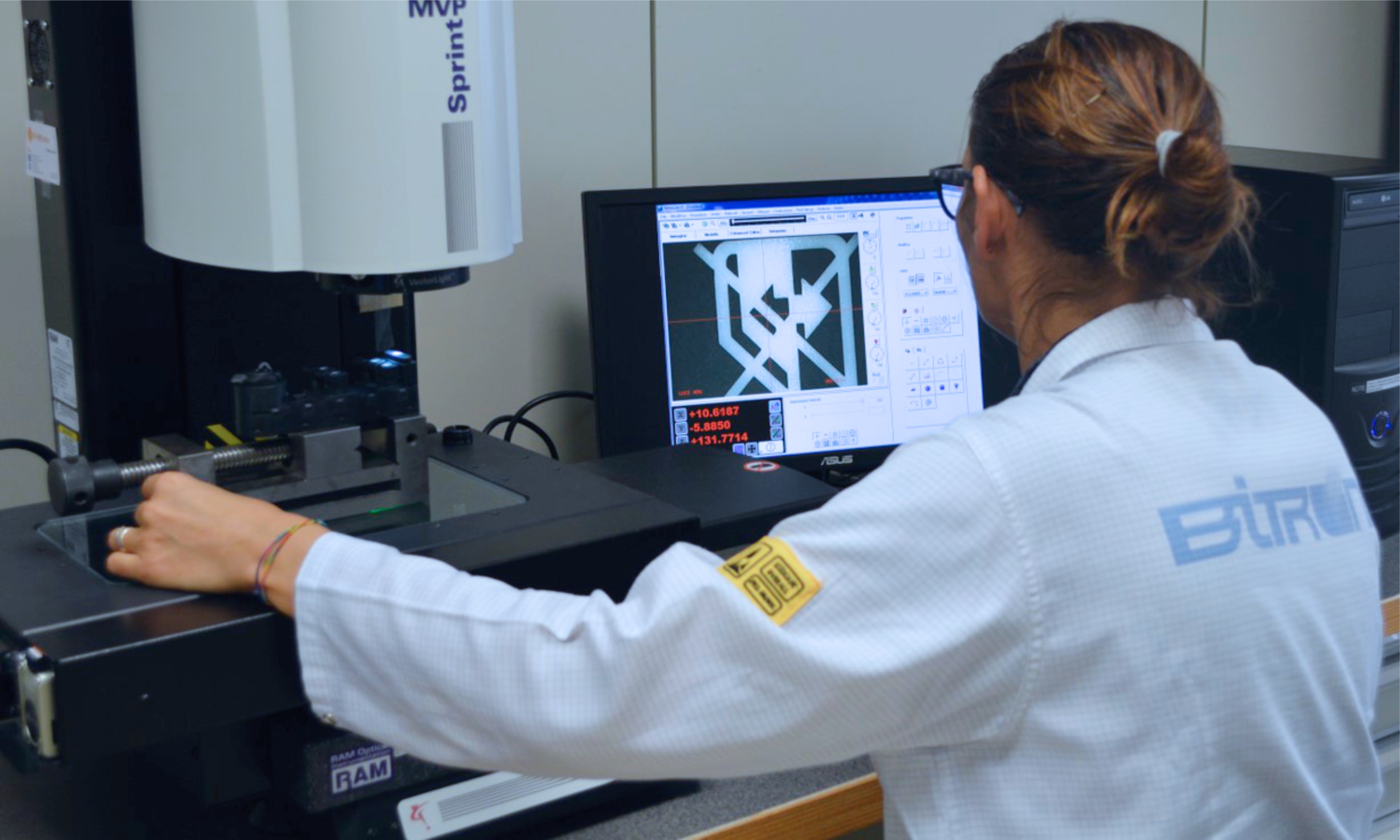